E-Sharp News
May 2024
Truly optimizing medical machining often requires specialized cutters, and there’s no better model for designing and grinding them than ARCH Cutting Tools, headquartered in Warren, Michigan, USA.
Take the task of machining a polyethylene tibial insert. As ARCH Cutting Tools’s northeastern regional director of operations, Jim Gray, spelled out, this has almost always been done with a single, flat blade mounted in a holder so as to maximize the shear angle. But, said Gray, this design often produces lines on the surface, or an “orange peel” effect, due to burning, as it doesn’t cut the polyethylene as cleanly as desired. A straight flute design also impacts the part with a lot of force on each rotation.
Gray’s team instead used their knowledge and ANCA’s programming software to create a unique 1½” (38.1 mm) diameter 3-flute carbide helical cutter with high shear and multiple radii along the profile. They grind it on an ANCA MX7 machine, using a dozen wheels to create a mirror finish and a cutting edge “sharper than a razor blade,” as Gray described it. “You need a very sharp edge to cut the plastic perfectly cleanly. Even a diamond grain that goes through cutting edge, leaving a tiny chip, will show up in the insert. We inspect these tools under a microscope to confirm the edge is crisp and clean.” Gray added that their helical design also distributes the cutting forces, in contrast to a straight flute. In sum, the ARCH Cutting Tools solution delivers an outstanding part finish, higher throughput, and longer tool life.
Replicating perfection
Gray also pointed out that in addition to the tool design assistance derived from ANCA’s programming software, which includes full 3D simulation, the ToolDraft feature enables detailed documentation for process control. “Instead of relying on 2D drawings on the shop floor,” Gray expounded, “ToolDraft gives us the ability lay out every aspect of the tool and the required grinding wheels. One page covers the gullet shape, with the roughing wheel, the finishing wheels, and any information related to fluting. The next page covers profiling, again with all the wheel shapes and data, and the required clearance angles, land width, and other tool geometries. And so forth for the end face. We also add notes to each drawing to provide detail on what’s pertinent to this tool…what really makes it work.
“We love what ToolDraft does for us. Because if all you put out on the floor is a 2D drawing with an outside diameter or shape of the tool, the operator can say ‘This tool is good. It’s to print,’ when in reality the body’s thin and the rake is not right. There are so many things that go into why we designed a tool a certain way, that if we don’t get complete information to the operator, everyone can have a different opinion about what constitutes a correct copy. We’ve promised our customers that no matter what person and what machine grinds their tool, they’ll get the same tool very time. And the only way we can keep that promise is with the documentation we’ve created with ToolDraft.”
Gray added that although it’s possible to grind such tools with a ball screw driven machine, it’s much easier to produce them with ANCA’s newer linear motor technology. “Linear motors have definitely changed our world when it comes to finishes and transitioning for profile cutters,” he explained. “They make it easier to grind the profile, especially with a tool like a condyle cutter, because multiple radiuses go up and over the edge. If you’re grinding in just one direction, a ball screw machine is fine. But if you go up and over and you need to produce multiple radiuses in the front and multiple radiuses in the back, that little backlash or wear in the ball screws will force you to fight until you get it all settled and tweaked in. Whereas with a linear motor machine, it’s just true from the start.”
Not all ball nose end mills are equal
Moving on to hip stems, Gray said machining up and over these parts requires ball nose end mills in which the radius and its transition to the OD must be perfect. The end face gashing must also meet exactly at the center. “Any mismatch in the center of the ball nose will put a line in the hip stem, and that’s not acceptable.” Any error in the radius will create geometrical distortion in the part profile, he added. “We scan that whole radius to ensure it’s correct.”
Hip stems have generally been made of titanium and cobalt chromium, Gray explained. These materials are challenging enough, but Gray said the new 3D printed titanium alloys from leading medical suppliers are even more difficult to machine. They’re porous, to facilitate integration with the patient’s bone, which essentially guarantees an interrupted cut. The material is also highly abrasive. Thus, minimizing tool changes and increasing manufacturing speed to achieve an acceptable level of efficiency requires an engineered solution from the likes of ARCH Cutting Tools.
Fast turn-around for custom tools and regrinds
In another example of ARCH Cutting Tools coming to the rescue, a customer suddenly ran out of an imported, replaceable head, keyseat cutter during production. ARCH Cutting Tools delivered a custom engineered, solid carbide version, with coating, in under 48 hours. In another case, ARCH Cutting Tools created a multi-step counterbore that combined 6 different operations in one tool for machining titanium and superalloys. Both examples again point to the power of combining experienced grinding professionals with ANCA’s software and machines to produce high quality medical devices that improve a person’s life.
Regrinding is yet another such area. Not only does ARCH Cutting Tools reliably return used tools to new condition, Gray said there are numerous cases in which they’ve actually improved upon the original tool. “One of our bigger medical customers was buying a faceted drill from one of the world leaders in cutting tools,” recalled Gray. “The drill was being used on titanium, and we put a roll point on it and made some other changes to the geometry that made the reground drill run better than the new tools.”
In this context, Gray praised ANCA’s integrated laser to automatically check for and correct errors in tool runout, and ANCA’s probing capability. In addition to probing coolant holes to ensure proper tool orientation for a regrind, Gray said ANCA makes it easy to probe the entire point profile to enable K-land grinding, a notoriously fiendish task. “You adjust how many points you want along that edge,” Gray expounded. “And if you’re manufacturing the tool, you can probe the profile once and store that data. From then on you don’t have to re-probe to produce a good K-land, until wheel wear becomes a factor.”
Wheel wear would cause the K-land to vary, Gray added, but he again pointed to the ease of re-probing the profile to make adjustments, plus the existence of wheel probes on their ANCA machines. “The wheel probe is absolutely awesome, because it takes human error out and it’s really accurate,” said Gray. The older method uses a measuring bar, and Gray recounted that operators all too often forgot which orientation they should use and destroyed an expensive wheel.
The science of productivity
As Gray put it, ARCH Cutting Tools has to be fast to be competitive, and that requires a process that’s “down to a science.” Things like matching different wheel specifications to the diverse tool materials they have to grind, proper coolant placement, and adaptable tool support. In the latter category, Gary praised ANCA’s P-axis traveling steadyrest and said that for some challenging applications they use an Arobotech, which grips the tool at 3 points and adjusts to changes in diameter as the P-axis moves below the grinding wheel, providing support. “These are all things that gives us an edge to be able to do these instruments,” Gray concluded. “They virtually eliminate runout and allow us to run faster.”
But Gray reserves his highest praise for ANCA’s simulation software, calling it “the greatest tool…We used to go to the machine blind. We’d end up scrapping blanks to figure out these complex tools right at the machine. With ANCA’s software, you create complex tools before going to the machine and you’re close to perfect when you run your first part.”
From creative tool design, to efficient machine setup and operation, to tight quality control, ARCH Cutting Tools consistently exemplifies what it takes to meet the challenges of machining medical components.

ARCH Cutting Tools produces a unique 3-flute carbide helical cutter that delivers unequaled part finish, higher throughput, and longer tool life in machining a polyethylene tibial insert

These ball nose end mills (for machining hip stems) feature a perfect transition from the ball radius to the OD, and an end face gash that meets exactly at the center

ARCH Cutting Tools delivered this custom engineered, solid carbide keyseat cutter, with coating, in under 48 hours

ARCH Cutting Tools created this multi-step counterbore to combine 6 different operations in one tool for machining titanium and superalloys
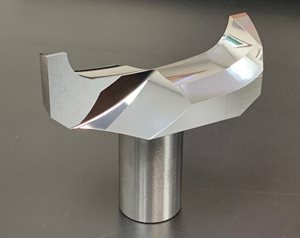
This complex trepan cutter was created to meet an urgent need for cutting non-ferrous material used in respiratory equipment. The tool features a very fine finish and leaves no marks on the part. Gray reported that “the customer was ecstatic”
5 March 2024